The Rise of Lathe Turning Parts Factories in Modern Manufacturing
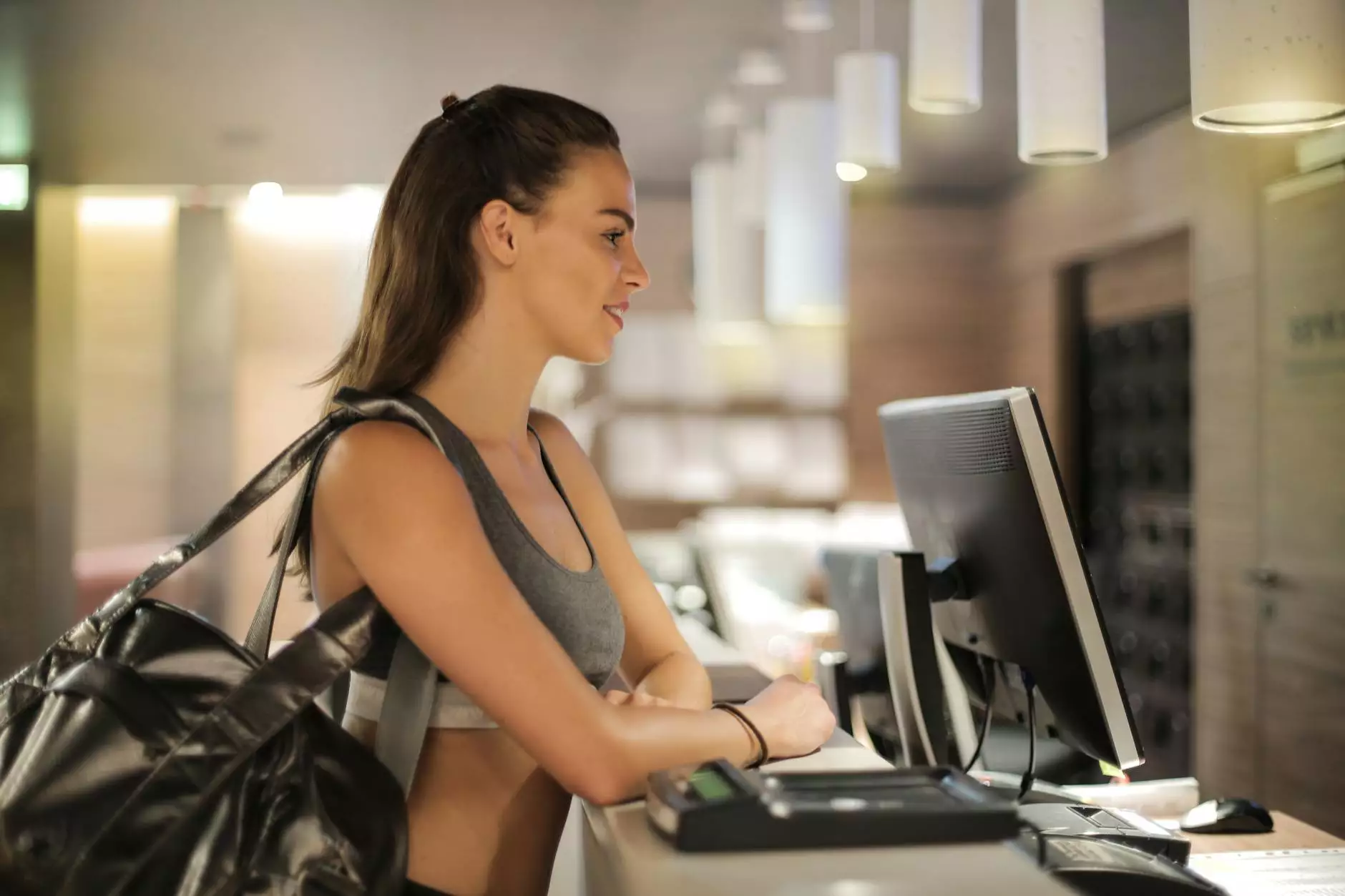
In today’s rapidly evolving industrial landscape, the lathe turning parts factory stands as a testament to the ingenuity and precision of modern manufacturing techniques. This article delves into the critical role these factories play in various sectors, their technological advancements, and why they are indispensable in the production of high-quality metal components.
What is a Lathe Turning Parts Factory?
A lathe turning parts factory specializes in machining various materials—primarily metals—using lathe turning techniques. Lathe turning involves the process of removing material from a workpiece to create a desired shape and size. This technique is fundamental in producing parts with high accuracy and repeatability.
The Process of Lathe Turning
Lathe turning is a subtractive manufacturing process, meaning it removes material to create the final product. The following steps outline the basic process:
- Material Selection: Choosing the right metal based on application requirements.
- Setting Up the Lathe: Installing the workpiece and configuring machine parameters.
- Machining: The lathe rotates the workpiece while a cutting tool removes material.
- Finishing: Adjustments such as sanding or additional machining to ensure precision.
Advantages of Using Lathe Turning in Manufacturing
The adoption of lathe turning technology in manufacturing yields numerous advantages:
- High Precision: Capable of producing parts with tight tolerances.
- Versatility: Ability to work with a variety of materials, including metals and plastics.
- Economical Production: Efficient use of materials reduces waste, leading to cost savings.
- Complex Shapes: Capable of producing intricate designs that are otherwise challenging to manufacture.
Key Features of a Lathe Turning Parts Factory
A lathe turning parts factory is equipped with advanced machinery that enhances the manufacturing process:
- CNC Lathes: Computer Numerical Control (CNC) lathes automate the turning process, increasing precision and reducing manual errors.
- Live Tooling: Incorporates additional cutting tools to perform multiple machining operations simultaneously.
- Quality Control Systems: Inbuilt inspection capabilities ensure that parts meet strict quality standards.
- Robust Tooling: High-quality cutting tools designed to withstand the rigors of metal machining.
Applications of Lathe Turning Parts
The applications of parts produced by a lathe turning parts factory are vast and varied, encompassing numerous industries:
Aerospace Industry
In aerospace, precision is paramount. Lathe turning is utilized to manufacture components such as:
- Engine parts
- Landing gear components
- Structural elements
Automotive Industry
The automotive sector relies heavily on lathe turning for producing:
- Transmission components
- Axles and shafts
- Custom fittings
Medical Devices
In the medical field, where precision can mean the difference between success and failure, lathe turning creates parts like:
- Implants and prosthetics
- Instrument components
- Measurement tools
The Future of Lathe Turning Parts Factories
As manufacturing technology continues to advance, the future of lathe turning parts factories looks promising. Innovations such as:
- Smart Manufacturing: Integrating IoT technology for real-time monitoring and optimization.
- Advanced Materials: Development of new alloys and composites that require precise machining techniques.
- Sustainability Practices: Implementing eco-friendly processes to minimize environmental impact.
Embracing Automation and AI
Automation and artificial intelligence (AI) are set to revolutionize the lathe turning parts factory environment. By leveraging AI, manufacturers can achieve:
- Enhanced predictive maintenance of machinery.
- Optimization of production schedules.
- Improved quality assurance through machine learning algorithms.
The Importance of Quality Control
Quality control in a lathe turning parts factory is critical to ensure the reliability and safety of manufactured components. Factors that contribute to quality assurance include:
- Regular Inspections: Conducting in-process inspections to catch defects early.
- Calibration of Equipment: Ensuring all tools and machines are calibrated to industry standards.
- Certification Standards: Adhering to ISO and other relevant industry certifications.
Collaboration with DeepMould.net
At [DeepMould.net](http://deepmould.net), our commitment to excellence in the field of metal fabrication enables us to provide unparalleled service in manufacturing precision lathe turned parts. By partnering with DeepMould.net, our clients benefit from:
- State-of-the-art machinery capable of producing complex parts.
- A skilled workforce trained in the latest machining techniques.
- Custom solutions tailored to meet specific project requirements.
Conclusion
The lathe turning parts factory represents a cornerstone of modern industrial manufacturing. From aerospace to medical devices, the precision and versatility offered by this process are unmatched. As we continue to innovate and adapt to changing technologies, the role of lathe turning will undeniably remain central to efficient production practices. Engaging with trusted partners like DeepMould.net ensures that you receive quality and precision in every component produced.
For those looking to enhance their manufacturing processes or to source high-quality lathe turned parts, establishing a partnership with a reputable lathe turning parts factory is essential. With advances in technology and a commitment to quality, the future of machining is brighter than ever.